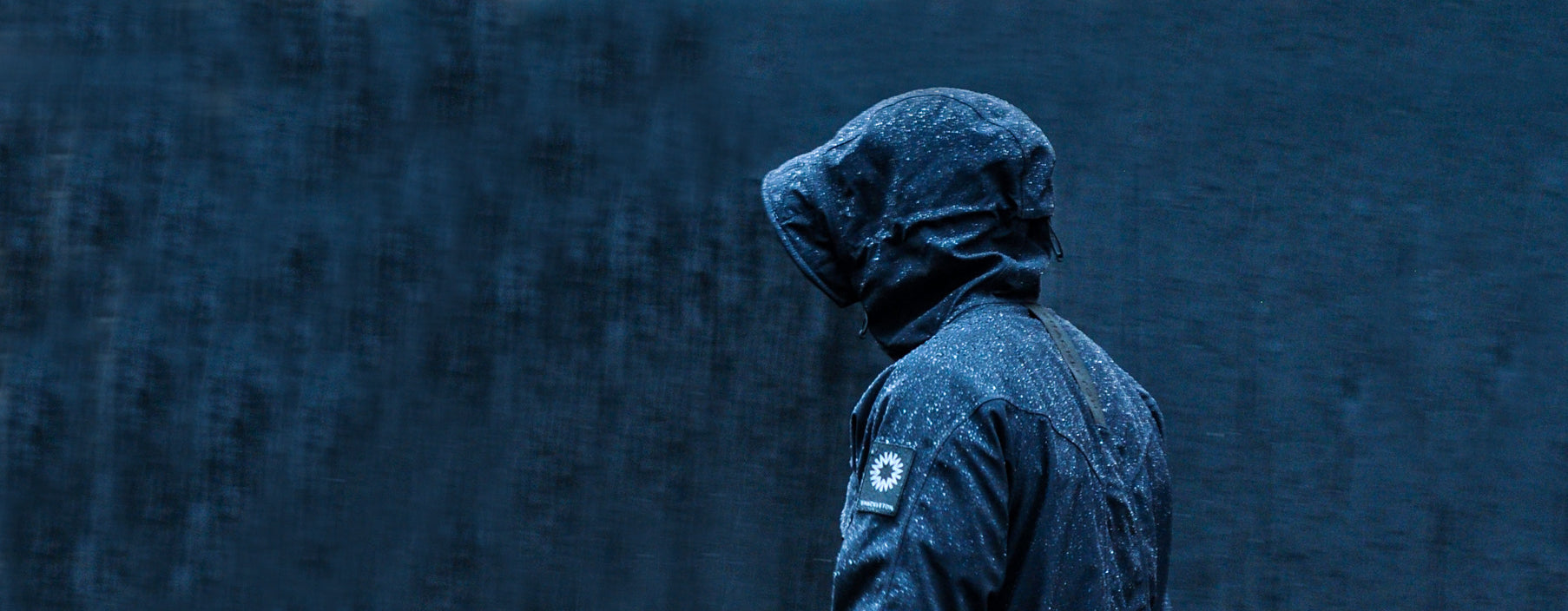
A SHACKLETON GUIDE TO WATERPROOFING
Technical waterproofing has come a long way since the first parkas were invented by the Caribou Inuit to keep warm in the Canadian arctic. Then parkas were made from seal or caribou skin and coated with fish oil for waterproofing. Fast forward to the era of our namesake, Sir Ernest Shackleton and the cutting edge of waterproofing technology in the 1800-1900s. Of course, the 'Boss' kitted out his crew with only the finest technical apparel available for this expeditions: a Burberry’s coat: tough-wearing, tightly-woven, and water-resistant. It was made from a twill gabardine fabric woven from Egyptian cotton waterproofed using lanolin both before and after weaving. These coatings were often heavy on the fabric and needed to be constantly reapplied.
Despite keeping Shackleton and his men alive when the 'Endurance' expedition, when the ship was trapped, drifting on the floes and eventually crushed by pack ice; during the treacherous crossing to South Georgia; and for those left behind on Elephant island, technological advancements in waterproofing have accelerated at an unprecedented rate since the turn of the century.
So how do we make waterproof jackets today and what technology is in place to create revolutionary waterproofing? Read on to find out all the details of contemporary waterproofing.
What Is The Difference Between 'Waterproof' and 'Water Resistant'?
Firstly we need to highlight the difference between ‘waterproof’ and ‘water resistant’. A true ‘waterproof’ jacket will feature a fabric which includes a thin waterproof membrane, a DWR coating and fully taped seams, keeping you protected from the heaviest downpour. A ‘water resistant’ jacket will have a DWR coating to help water bead off the fabric in light showers.
A waterproof laminate is created using a fine membrane that is made separately as a sheet of material, which is then glued or bonded (laminated) to the face fabric. It is important to select and pair the right membrane with the correct fabric and bonding process for the fabric’s ultimate intended use. Membrane fabrics are engineered to allow some moisture, like sweat, to pass through them, resulting in a more breathable and therefore, comfortable coat.
Then a liquid is applied to the fabric to form a flexible, durable waterproof coating (DWR).
How a Waterproof Fabric is Built
Waterproof fabrics, whether coated or laminated, are usually constructed in one of three ways. Each method results in different characteristics and possible uses.
2-Layer
A 2-Layer has the simplest waterproof fabric construction with a laminated or coated membrane being applied to a single layer of fabric.
2-Layer waterproof fabrics are generally the lightest in weight, ideal for situations where low weight and packability are crucial. They are often used in lightweight waterproof jackets, where there is no direct abrasion on the membrane.
2.5-Layer
A 2.5-layer construction is similar to a 2-layer construction with the addition of a light coating or print, which is applied to the surface of the membrane.
This additional coating protects the membrane without affecting the breathability, as well as adding softness against the skin. 2.5-layer fabrics are relatively packable.
3-Layer
A 3-layer waterproof fabric is the most complex to manufacture. In this type of construction the membrane is sandwiched between an outer (face) fabric and an extremely light woven or knitted inner (backer) fabric. The third layer offers more comfort, durability and protection.
3-layer construction is commonly found in hardwearing and durable shell garments which are still lightweight and relatively packable, as well as in insulated parkas.
Durable Water Repellent Treatment
A durable water repellent treatment (DWR) is a treatment often applied to the outer face fabric to help maintain the waterproofness and breathability and to ensure the membrane works as efficiently as possible. Without a DWR coating most fabrics will absorb water or rain.
A DWR coating can applied in the absence of a waterproof membrane to produce a lightweight water resistant garment, it also helps add durability to fabrics such as the 100% recycled Japanese ripstop found in the Rothera, Ronne and Ross.
The main function of a DWR treatment is to keep the fabric dry by causing water droplets to bead up on the surface.
In the case of a membrane fabric, keeping the face fabric free from standing water allows the membrane to breath and to move moisture to the outside without encountering any barriers such as water that’s soaked into the face fabric.
Underneath the microscope DWR looks like pillars standing up away from the fabric’s surface, they are close enough together to stop water droplets being able to sit on the face fabric itself but wide enough apart that water vapour molecules from underneath are able to pass through the membrane and then out through the fabric.
Depending on activity and frequency of use these pillars can get flattened over time, reducing the efficacy of the DWR.
For those seeking a more environmentally friendly jacket, look out for C0 finishes as an alternative to chemicals used in PFC and FC coatings. C0 DWRs break down naturally in the environment without leaving toxins in the water or soil. Learn more here.
What are PFCs?
PFCs, also known as perfluorocarbons, polyfluorocarbons and fluororesins, are compound chain chemicals that historically, have been widely used in the outdoor apparel industry to repel water, dirt and oil from fabric surfaces.
C8 chemistry has been used on outdoor apparel fabric for durable water repellency (DWR) for years. This chemical contains PFOA and PFOS long chain compounds which don’t break down. Over time they have built up in the air and water systems, ultimately finding their way into the food chain, posing a harmful threat to both wildlife and humans. These chemicals have been linked to immune system reduction and are also carcinogenic. They have since been banned by REACH amongst other legal bodies.
C6 and C0 chemistry replaced C8 chemistry as a less harmful solution.
Over the last few years the chemistry industry has invested a lot of time and effort into the innovation of PFC-free (C0) DWR finishes which do not contain any harmful chemicals.
The highly respected Rudholf Group created Bionic Finish® ECO DWR, taking inspiration from nature, the chemicals used have branchlike structures that crystalise to create a strong bond repelling water without the need for PFCs. This DWR is bluesign® certified and used to treat our Escape Down Jacket.
We also use PFC-free C0 DWR coatings for the Markham Hardshell Jacket, Haakon Tactical Parka, Endurance Lightweight Parka, Rothera Down Jacket, Ronne Down Jacket and Ross Down Gilet.
What are PTFEs?
Similar to PFCs, PTFEs are long chain chemical compounds used in membranes that are laminated to fabrics to create ultimate waterproofing. They also do not break down and cannot be recycled and share the same harmful impacts to the environment and living beings as PFCs. No Shackleton fabrics use PTFEs.
What is Hydrostatic Head Rating?
Across Shackleton outerwear you will see ratings waterproofing ratings measured in mm. This refers to the Hydrostatic Head (H/H) rating of a fabric.
Hydrostatic Head is the test method that is used to describe the amount of water pressure a fabric can withstand.
Imagine a 30 metre tube sitting on top of a fabric’s surface. The tube is slowly being filled with water and as more and more water is added the pressure on the fabric increases. The Hydrostatic Head test results are expressed as the height of the water column that the fabric can withstand before water is able to pass through (so 20,000mm equals a column 20m high). Rather than a long tube, a Hydrostatic Head machine is used. The machine clamps a sample of the fabric in place and then forces water onto that fabric that simulates the height of the water column.
In the field water pressure comes from a wide array of places. From the size and speed of raindrops in a thunderstorm to abrasion from backpack straps, climbing harnesses, or even kneeling on the ground. All these exert water pressure on the fabric. Sitting on the ground for example could exert 1,500-2,000mm whereas kneeling in the same spot could exert up to 10,000mm because of the reduction in surface area exposed to the water.
Which rating is best suited to which conditions?
5,000mm - Usually regarded as the lowest threshold for a ‘waterproof’, 5,000mm will be sufficient in little to no rain, but can’t be relied on in a heavy shower.
10,000mm - A strong choice for more extreme excursions as it will protect you in high impact, heavy showers and downpours. A 10,000mm fabric is a strong all-rounder for your go-to waterproof jacket, effective in a range of conditions.
20,000mm - Able to withstand high pressure rain and the very worst weather conditions. Often a 20,000mm waterproof jacket boasts fully waterproof taped seams and zips with a multi-layered fabric.
Shackleton parkas require a 10,000mm (H/H) rating or above, though many have a 20,000mm (H/H) rating.
Durability
We ensure that exhaustive durability tests are carried out independently by Intertek. There is a vast array of properties we can test for, but abrasion, tear strength and tensile strength are key metrics for durability.
Abrasion
We make the most of the Martindale method which offers an industry standard test for durability. The Martindale machine simulates long term wear in the form of the pressure an item will have on the fabric, like the constant abrasion of wearing a heavy backpack.
For the test to be carried out the shell fabric is cut into specific sized circles and inserted into the testing machine. The machine replicates abrasion by rubbing across the sample with a set pressure and in a specific pattern. The sample is checked at predetermined intervals until it reaches the end point.
The end point can be different depending on the type of fabric but can include:
- Fibre breakage
- Holes
- Weight loss
- Worn-out pile
- Other appearance changes
The results are either reported in rubs or cycles - these are the same result with different labels. It will give an indication of how durable the fabric will be during continued wear and use.
Tear Strength
Tear strength is testing for how well a fabric can withstand a sudden force. The higher the tear strength, the more the fabric can withstand high activity use without breaking.
To test the tear strength, the fabric is secured into the machine by the edges and a weighted pendulum is dropped to simulate sudden force and cause a single-rip tear in the fabric. The machine records the amount of force needed to create the tear. This is repeated using both the warp direction and the weft direction, giving two results.
Tensile Strength
Tensile strength is a great indicator of how durable a fabric will be during repeated use. The higher the tensile strength, the more the fabric can withstand gradual strain or repeated use without stretching out of shape or breaking.
To test a fabric's tensile strength a strip of fabric is secured by the edges in the test machine and force is applied in increments by pulling at each edge of the fabric. The force is increased until the fabric ruptures or is significantly elongated. This will also be tested with the strips of fabric in warp direction and weft direction, giving two separate results.
If you were wearing a pair of trousers, high tear strength fabric will mean if you suddenly dropped to your knees or in a squat, it won't rip. High tensile fabric maintains its shape with no breakage over all the strain of walking, bending, stretching etc. over continued use.
At Shackleton we tailor our fabric requirements towards the end use of the garment but the majority of Shackleton fabrics have both high tear and tensile strength ratings.
We also test our kit for durability extensively in the field. Our Shackleton Challenges Expedition team lead year round trips to the world’s most extreme and remote locations, always wearing the latest Shackleton designs to test for durability, performance and fit.
This means that Shackleton performance apparel has undergone numerous rounds of refinement with feedback from some of the world’s finest polar explorers. Louis Rudd and Wendy Searle’s feedback to the product team ensures that every aspect, from construction to fit, is working correctly.
EXPLORE WATERPROOF JACKETS
From down insulated parkas to storm-proof shell jackets, you'll find the waterproof jacket you need, in the Shackleton collection, found HERE.
TRY BEFORE YOU BUY
Drop into our London store (214 Piccadilly, W1J 9HL) to explore the range. All information can be found HERE.
GET IN TOUCH
Want to learn more? Call us on +44 (0) 208 138 0212 or email info@shackleton.com to talk to a member of our team, who will happily assist you.